Investing in Safety
Along with being Earth’s Most Customer-Centric Company and Earth’s Best Employer, we’re also committed to becoming Earth’s Safest Place to Work.
We ensure that safety is at the heart of everything we do. That’s why we invest millions every year in training and technology to help our people stay safe while doing their job.
We ensure that safety is at the heart of everything we do. That’s why we invest millions every year in training and technology to help our people stay safe while doing their job.
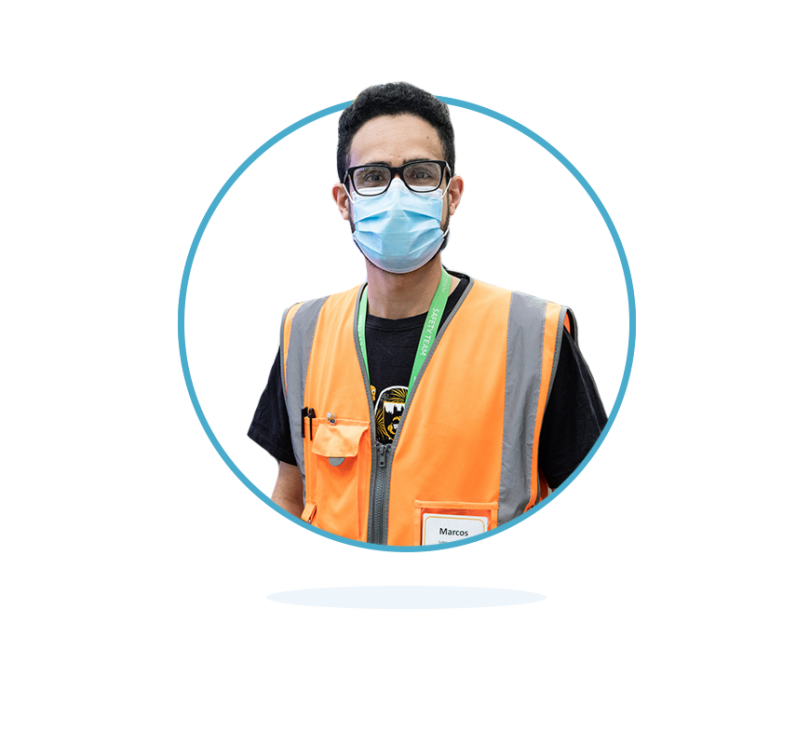
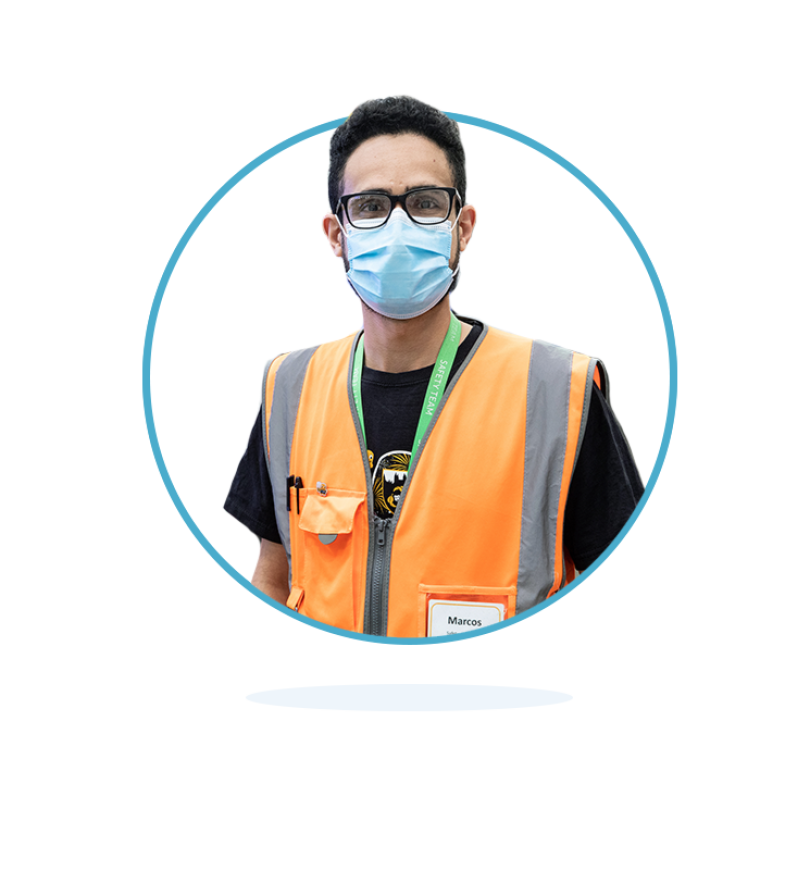
Investing in safety
Our safety training, coaching, and engagement inspires everyone working at Amazon to share ownership in creating a safe workplace.
All photos of people not wearing masks were taken prior to the COVID-19 pandemic.
All photos of people not wearing masks were taken prior to the COVID-19 pandemic.
Safety experts are vital to our business
We employ more than 200 qualified and experienced safety professionals and during 2020, we conducted more than 400,000 safety compliance inspections across our UK operations. If our safety teams find anything wrong, they recommend actions that are then followed up by senior managers.
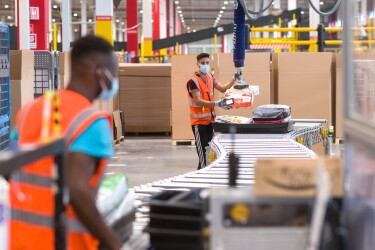

Designed for safety from the start
We take safety into account in all aspects of our operations, from initial site and process design to training. Safety rules are communicated prominently from the moment anyone—employee or visitor—arrives at one of our fulfilment centres. There are extensive safety signage and hazard warnings throughout every site, including no-step zones beyond safe walkways and flashing hazard lights on all moving equipment. Potentially hazardous machinery incorporates safeguarding measures where required, such as pedestrian proximity radar warnings for moving vehicles and user proximity shutdown and disable mechanisms on automated equipment. We enforce mandatory use of necessary Personal Protective Equipment (PPE) in all working areas across all sites.
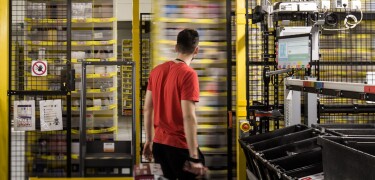
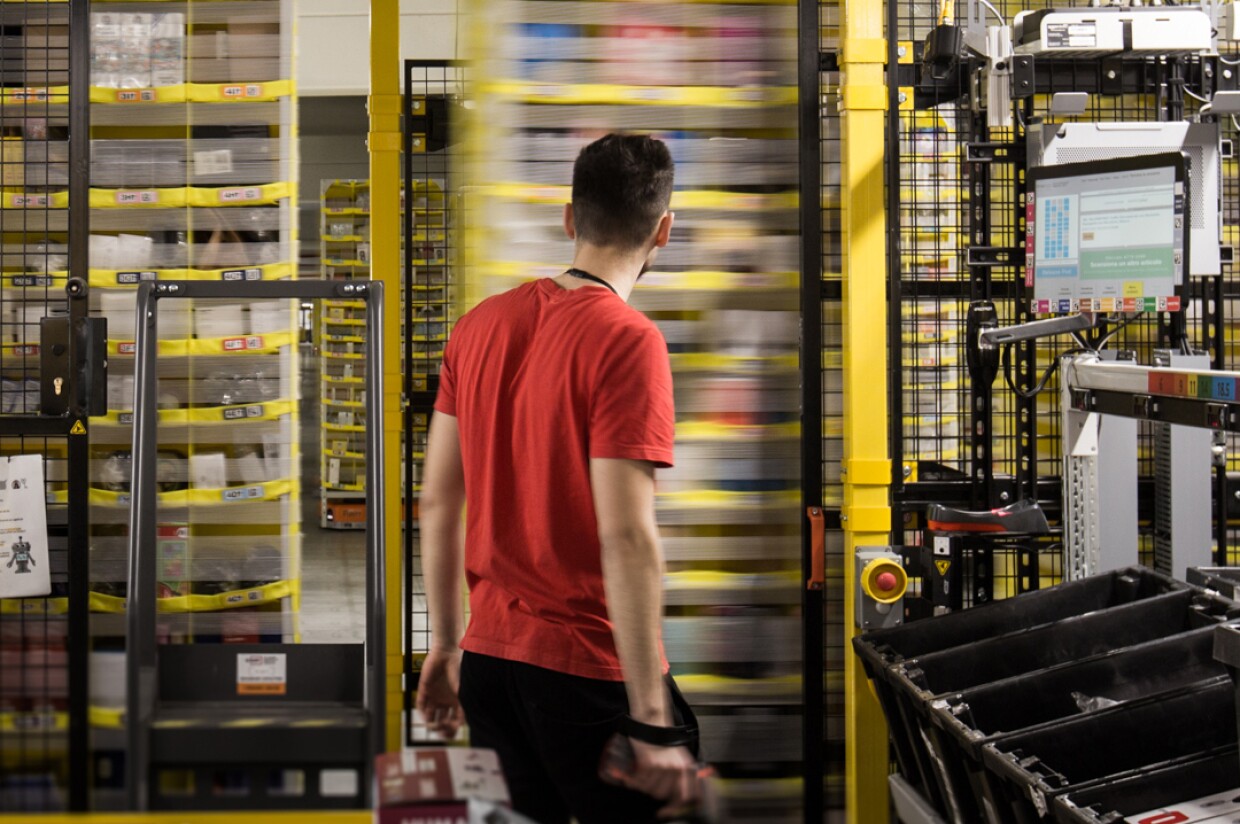
Amazon has a strong leadership commitment to safety, which we emphasise in all management communications to reinforce the importance of keeping people safe at work every day. Under our Safety Circles programme, every manager in each fulfilment centre is required to “walk the floor” every week and engage with up to five employees—selected randomly from the employee database—to gather their views on safety.
Each fulfilment centre has a comprehensive management plan reflecting the latest UK Health and Safety Executive (HSE) guidance, International Labour Organization OSH-2001 Guidelines, and other relevant standards and best practices.
Each fulfilment centre has a comprehensive management plan reflecting the latest UK Health and Safety Executive (HSE) guidance, International Labour Organization OSH-2001 Guidelines, and other relevant standards and best practices.
Dedicated safety training
Every single person who joins Amazon receives regular dedicated safety training from day one and every internal meeting begins with a safety tip. We also encourage a reporting culture that requires all potential risks and incidents—however minor—to be formally logged for analysis and action.
We monitor safety performance constantly. Detailed safety-related metrics are a key performance indicator in all senior management meetings. They're reviewed weekly at site level and monthly at UK and European leadership level.
We monitor safety performance constantly. Detailed safety-related metrics are a key performance indicator in all senior management meetings. They're reviewed weekly at site level and monthly at UK and European leadership level.
Protecting through the pandemic
Keeping our people safe through the COVID-19 pandemic remains our top priority.
We committed $11.5 billion worldwide in 2020 on COVID-related initiatives to help keep our employees safe and to get items to customs. This included an investment of over $1.2 billion on measures like temperature checks, masks, gloves, enhanced cleaning and sanitation, testing and more. To ensure we were constantly keeping our team safe, we also implemented over 150 significant process changes, including social distancing measures and enhanced cleaning and sanitizing across every site.
We committed $11.5 billion worldwide in 2020 on COVID-related initiatives to help keep our employees safe and to get items to customs. This included an investment of over $1.2 billion on measures like temperature checks, masks, gloves, enhanced cleaning and sanitation, testing and more. To ensure we were constantly keeping our team safe, we also implemented over 150 significant process changes, including social distancing measures and enhanced cleaning and sanitizing across every site.
Employee Safety
In the UK alone, we’ve provided our employees with:
-
95,000,000 face masks
-
2,453,000 litres of hand sanitiser
-
155,715,791 pairs of gloves
-
480,000,000 sanitary wipes
All photos of people not wearing masks were taken prior to the COVID-19 pandemic.
All photos of people not wearing masks were taken prior to the COVID-19 pandemic.
Reporting on safety
Risk and incident reporting are a critical aspect of maintaining effective safety management systems. We encourage employees to report any incident—however seemingly minor or trivial. We also encourage employees to report any situation or event that had the potential to cause harm.
Every report is analysed by members of our safety team, who bring in additional technical expertise if required to address a specific identified risk. We constantly monitor and evaluate incident and HIPO data, and if we spot an emerging pattern of specific incidents or risks, we take prompt action.
Every report is analysed by members of our safety team, who bring in additional technical expertise if required to address a specific identified risk. We constantly monitor and evaluate incident and HIPO data, and if we spot an emerging pattern of specific incidents or risks, we take prompt action.
Nothing is more important to us than the safety of our people.
We benchmark against UK national data, published by the Health & Safety Executive, which confirms we have over 40% fewer injuries on average than other transportation and warehousing businesses in the UK.
Investing in technology to make things even safer
Our technology helps to reduce the physical demands on our employees. Some of these technological solutions are detailed below:
-
RoboticsRobotics units handle the majority of products in our Amazon robotics fulfilment centres and reduce the physical demands on our employees. The units bring products directly to employees, who then pick and stow customer orders.
-
Intelligent VestsIntelligent vests worn by employees use short-range radio frequencies to send signals to robotics units to slow down, alter their work, or stop when they detect employees.
We work with delivery service providers and their drivers to integrate safety into every stage of a package’s journey.
Beyond our fulfilment centres, our delivery network is powered by thousands of small businesses and tens of thousands of drivers who rely on Amazon’s technology and safety initiatives every day.
Our custom electric vehicles are fitted with a range of safety, navigation, and design features. The features include state-of-the-art sensor detection, highway and traffic assist technology, exterior cameras linked to internal digital display for 360-degree visibility, and Alexa-integrated hands-free route and weather information.
Our custom electric vehicles are fitted with a range of safety, navigation, and design features. The features include state-of-the-art sensor detection, highway and traffic assist technology, exterior cameras linked to internal digital display for 360-degree visibility, and Alexa-integrated hands-free route and weather information.
"I've been out of industry for 18 years and thought it would no longer interest me—but the juices have started flowing again! It's a fascinating company, I appreciate the challenge, really enjoy meeting my colleagues, and am constantly impressed by the way the fulfilment centre is managed. The way Amazon has adapted its operation because of coronavirus to take care of employees and still deliver for customers is amazing. Apart from my own home, it's the safest place I've been. I'll be honest—I joined Amazon because it was a way of providing an income but, even in a matter of weeks, it's provided me with so much more."
Paul McKiePaul owns a photography business and was previously a senior company director. He joined Amazon in 2020 as a temporary associate in Rugby fulfilment and has quickly been promoted to area manager.